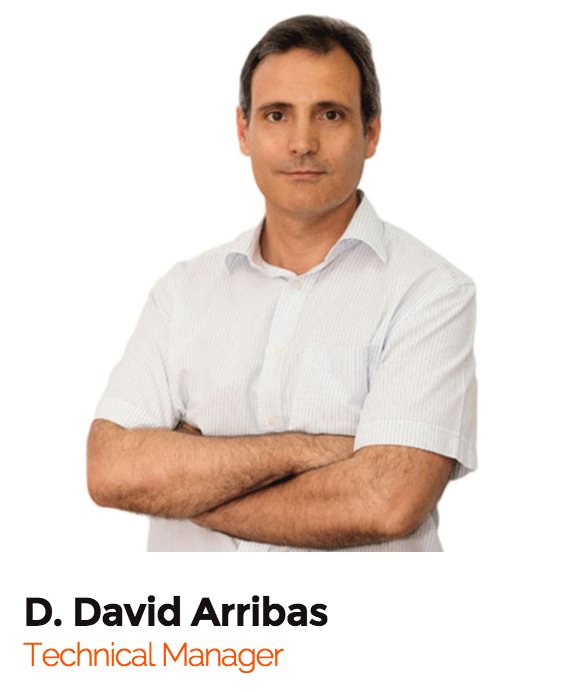
We commence a new series of interviews with our people. A way to get acquainted with the persons who stay behind each and every solution TEC offers. In our next interview we have the pleasure to present you David Arribas – Technical Director
Question:
To be before the team that researches, designs and develops new products must mean continuously having to keep informed about news and customers’ needs. How do you prioritise customers’ demands given the requests for products to have new functionalities?
Answer:
TEC Container is a little family in which teamwork is fundamental. The Technical Department is one piece in a well-oiled machine, which tries to solve the problems detected by our customers, offering a good solution as inexpensively. Prioritising these demands is not only a matter for the Technical Department. This is a decision taken jointly with both the company management and with the Commercial Department and for which our customers’ satisfaction is our only priority.
Q:
The port loading and lifting sector is evolving, as regards the machinery that is used, at a great pace. Do you think these changes are due to globalisation and the immediacy that customers demand, or are they the consequence of other factors?
A:
In reality, the port loading and lifting sector has been, throughout history, one of the most reluctant to change. Apart from globalisation and the immediacy demanded by customers, the liberalisation of the sector and competence, is what has greatly increased the need for investments to be more competitive.
Q:
Quality and safety are two of the words that are always associated with the products of the TEC Container families. When designing new solutions, are these factors subordinate to design or is it design that adapts to the factors?
A:
If there is something that’s non-negotiable in a TEC Container design it is safety. And quality is fundamental to differentiate us from other companies in much more competitive economic areas in such a globalised world as this. When somebody purchases a TEC Container product they know that those two factors are guaranteed.
Q:
It is easy to imagine the technical team in front of computer, sketching and designing, but to what extent do you think that being in a port terminal watching the machines’ work is as important at design in front of a computer?
A:
Design in front of a computer is important; but it is only a small part of our work. No matter how much the three-dimensional simulation and design programmes have been modernised; only in direct contact with the factory and to a greater extent with maintenance and stow staff in the terminal, may lead us to deal with problems that we really know about.
Q:
The design of a building or an automobile is better known due to their popularity in relation to the load and lifting solutions. How long does the design and creation of a new product take?
A:
It depends a great deal on the product. TEC Container is continuously innovating, designing and improving. We have some who only need a few hours for adjustment or inclusion of small details. Others that take months or even years from the initial idea to the completed product.
Q:
One of the features of TEC Container is the customers’ option of customising products to obtain the ideal solution. Does this entail a challenge when designing the basic pieces of each product?
A:
The main challenge is to achieve this at competitive prices. Many companies carry out bespoke work, but very few manage such high standards of quality and safety as such competitive prices. The main secret is to have a team of people with great experience, imagination and love for their work.
Q:
In the years you’ve been at TEC Container you’ve designed several products with your team. Which do you consider was a breakthrough in the sector as regards innovation?
A:
The first OHFs (Over Height Frames) more than 20 years ago entailed an enormous improvement as regards handling of outsized loads. This eliminated manual attachment of chains and there enormously increase both the stevedore’s safety and the speed of operations. First, we designed the manual models, a few years later we went on to semi-automatic and fully mechanical direct transmission systems (delay). But now with the design of fully autonomous and universal solar electric systems, a product has been achieved that is clearly leading in the sector. This continuous improvement in our product, year after year, has made it a model to follow; beating all its competitors’ products and being the design to copy for some infinitely larger and more powerful brands.
Q:
And lastly, what is the product, solution or innovation of which TEC has been part of which you’re proudest?
A:
All the products we design are important and we’re fond of them, but safety cages have always been an old challenge. Firstly because of the need to eliminate an enormous danger thousands of stevedores faced daily, by literally climbing on piles of containers to unlash or unblock them. Secondly, due to achieving, with the help of a great many people in the sector and the direct involvement of the whole company, to fill something of the legal vacuum with which we were confronted when they were designed. This has culminated with the publication, by the National Institute of Safety and Hygiene, of HSN 1.083 which begins this necessary regulation.
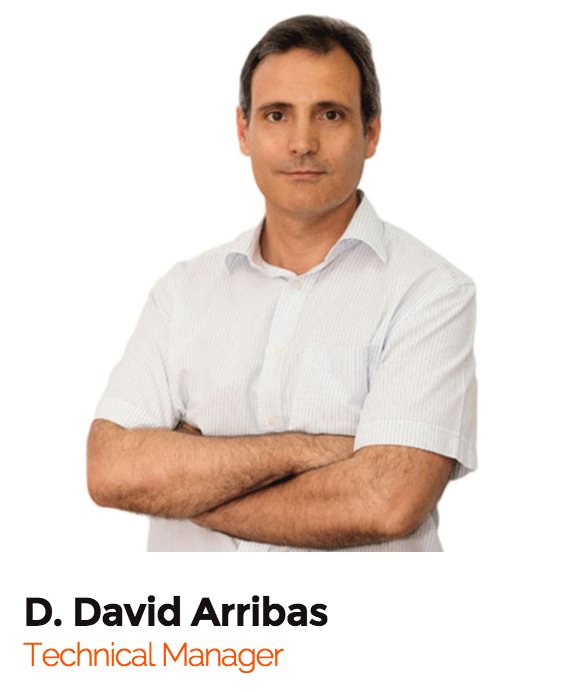