It is important that a company which bases its future on innovation always keeps an eye on new technologies. The inclusion of new technological tools in the day-to-day work is a permanent task. This is the case of 3D printing of tailor-made parts and spares.
In April 2018, TTS OFFSHORE appointed TEC Container to design and manufacture a 40-foot Spreader certified to work in an ATEX environment, that is, an electric spreader for use in a potentially explosive environment. In this occasion, it is the warehouse of a ROPAX boat powered by Liquefied Natural Gas.
During the stage of design, prototype development and the subsequent manufacture with a view to the ATEX certification, one of the many points to take into account was that it was necessary to prevent the contact of the electrical wiring with the metallic areas of the main structure and that was where we realized that we could design and then print in 3D the parts of the cable glands.
THREE FUNDAMENTAL STEPS: DESIGN, PROTOTYPING AND INSTALLATION.
1.- DESIGN.
The piece is composed of two non-symmetrical parts that adapt to the available space in the beams of the spreader. These were not available commercially so they were designed in 3D CAD SOLIDWORKS software and later prepared in the CURA 2.1.2 program of Ultimaker BV.
2.- PRINTING AND INSTALLATION OF THE PROTOTYPE.
To make sure that the design is correct and the adaptation to the space available in the spreader is perfect, we proceeded to print a prototype in disposable material. Said material is PLA (Polyacid lactic acid) and the printer used is SIGMA R19 (BCN 3D).
3.- IMPRESSION AND FINAL INSTALLATION.
Finally and after checking that the design is correct, we printed the final version on ASA material (Acrylonitrile Styrene Acrylate). We choose this material for its technical characteristics of resistance to ultraviolet rays, extreme temperature resistance, rain … etc.
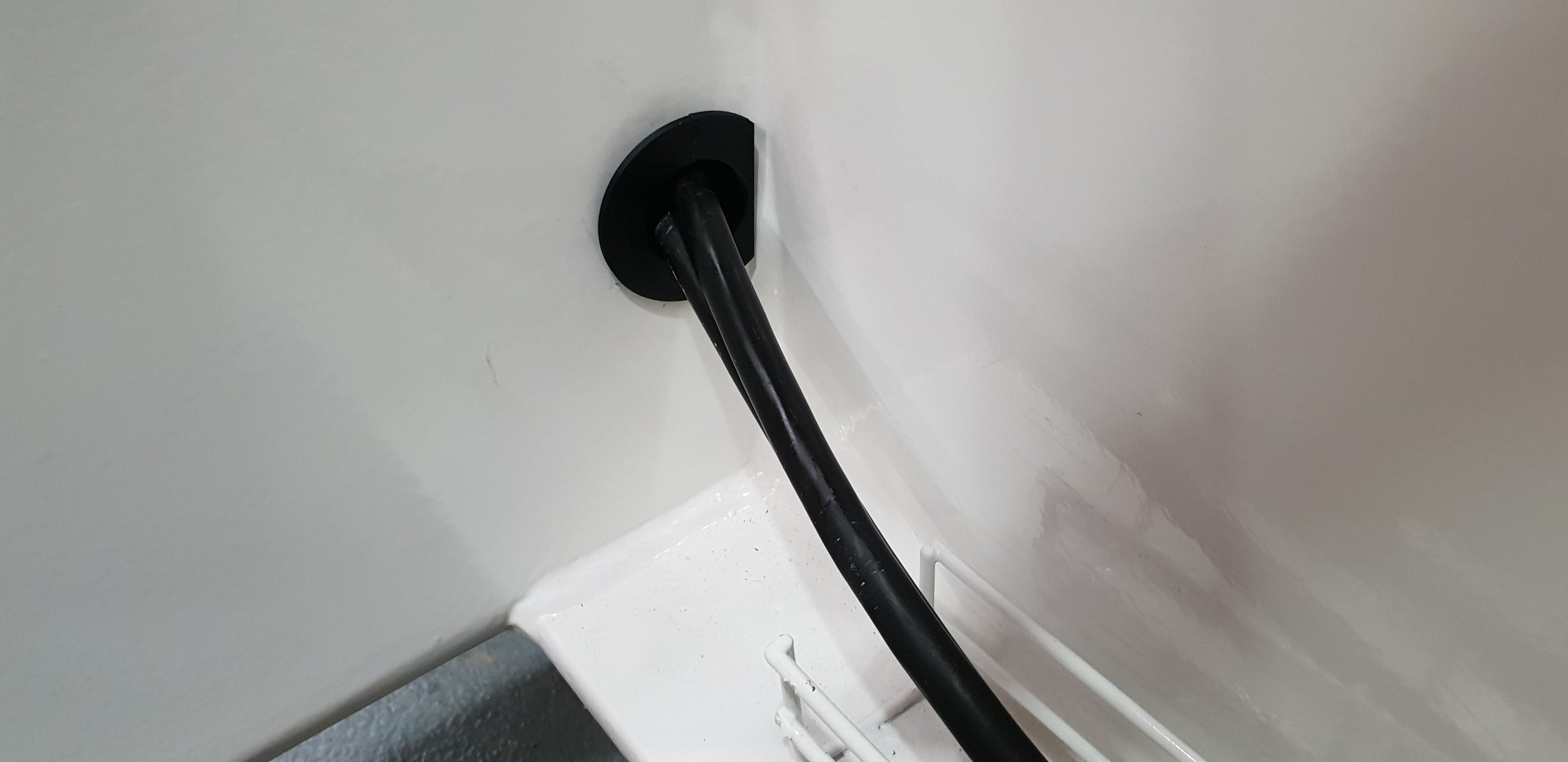
More information at teccontainer.com